|
Classification of plastic bottle
A plastic bottle is a bottle constructed from plastic. Plastic bottles are typically used to store liquids such as water, soft drinks, motor oil, cooking oil, medicine, shampoo, milk, and ink. The size ranges from very small sample bottles to large carboys.
Plastic bottles are formed using a variety of techniques. The choice of material varies depending upon application.
High Density Polyethylene (HDPE) is the most widely used resin for plastic bottles. This material is economical, impact resistant, and provides a good moisture barrier. HDPE is compatible with a wide range of products including acids and caustics but is not compatible with solvents. It is supplied in FDA-approved food grade. HDPE is naturally translucent and flexible. The addition of color will make HDPE opaque, but not glossy. HDPE lends itself to silk screen decoration. While HDPE provides good protection at below freezing temperatures, it cannot be used with products filled above 160 ¡ãF (71 ¡ãC) or products requiring a hermetic (vacuum) seal.
Low Density Polyethylene (LDPE) is similar to HDPE in composition. It is less rigid and generally less chemically resistant than HDPE, but is more translucent. LDPE is used primarily for squeeze applications. LDPE is significantly more expensive than HDPE.
Polyethylene Terephthalate (PET, PETE or polyester) is commonly used for carbonated beverage, water bottles and many food products. PET provides very good alcohol and essential oil barrier properties, generally good chemical resistance (although acetones and ketones will attack PET) and a high degree of impact resistance and tensile strength. The orienting process serves to improve gas and moisture barrier properties and impact strength. This material does not provide resistance to very high temperature applications¡ªmax. temp. 200 ¡ãF (93 ¡ãC).
Polyvinyl Chloride (PVC) is naturally clear, has extremely good resistance to oils, and has very low oxygen transmission. It provides an excellent barrier to most gases and its drop impact resistance is also very good. This material is chemically resistant, but it is vulnerable to some solvents. PVC has poor resistance to high temperatures and will distort at 160 ¡ãF (71 ¡ãC), making it incompatible with hot-filled products. It has attained notoriety in recent years due to potential health risks.
Polycarbonate (PC) is a clear plastic used to make water and milk bottles. 5 gallon water bottles are the most common examples of PC bottles.
Polypropylene (PP) is used primarily for jars and closures and provides a rigid package with excellent moisture barrier. One major advantage of polypropylene is its stability at high temperatures, up to 220 ¡ãF (104 ¡ãC). Polypropylene is autoclavable and offers the potential for steam sterilization. The compatibility of PP with high filling temperatures is responsible for its use with hot fill products. PP has excellent chemical resistance, but provides poor impact resistance in cold temperatures.
Polystyrene (PS) offers excellent clarity and stiffness at an economical cost. It is commonly used with dry products including vitamins, petroleum jellies, and spices. Styrene does not provide good barrier properties, and exhibits poor impact resistance.
Fluorine Treated (HDPE) bottles are exposed to fluorine gas in a secondary operation, are similar in appearance to HDPE and have exceptional barrier properties to hydrocarbons and aromatic solvents. Fluorine treated bottles are excellent for use with insecticides, pesticides, herbicides, photographic chemicals, agricultural chemicals, household and industrial cleaners, electronic chemicals, medical cleaners and solvents, citrus products, d-limonene, flavors, fragrances, essential oils, surfactants, polishes, additives, graffiti cleaning products, pre-emergents, stone and tile care products, waxes, paint thinner, gasoline, biodiesel, xylene, acetone, kerosene and more. For non-bottle applications, fluorination of plastic can provide compliance with state and federal regulations. An example would be fluorination plastic fuel tanks used for lawn and garden equipment, automobiles, etc.
Post Consumer Resin (PCR) is a blend of reclaimed natural HDPE (primarily from milk and water containers) and virgin resin. The recycled material is cleaned, ground and recompounded into uniform pellets along with prime virgin material especially designed to build up environmental stress crack resistance. PCR has no odor but exhibits a slight yellow tint in its natural state. This tint can be hidden by the addition of color. PCR is easily processed and inexpensive. However, it cannot come into direct contact with food or pharmaceutical products. PCR can be produced in a variety of recycled content percentages up to 100%.
K-Resin (SBC) is ideally suited to a wide variety of packaging applications by virtue of its sparkling clarity, high gloss, and impact resistance. K-Resin, a styrene derivative, is easily processed on polyethylene equipment. It is suitable for packaging many products but is specifically incompatible with fats and unsaturated oils or solvents. This material is frequently used for display and point-of-purchase packaging. Bioplastic - polymer structures based on processed biological materials rather than petrochemicals. Bioplastics are commonly made from renewable sources like starch, vegetable oil, and less commonly, chicken feathers. The idea behind bioplastic is to create a plastic that has the ability to biodegrade.
|
|
|
|
Good News! Infullpak company had installed 3D printer to meet the customer's requirement quickly.If you need to develop the new mould or do some pilot production please contact us!
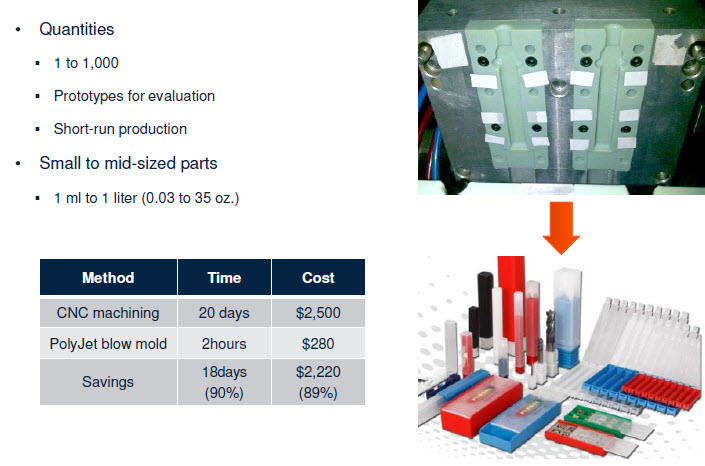

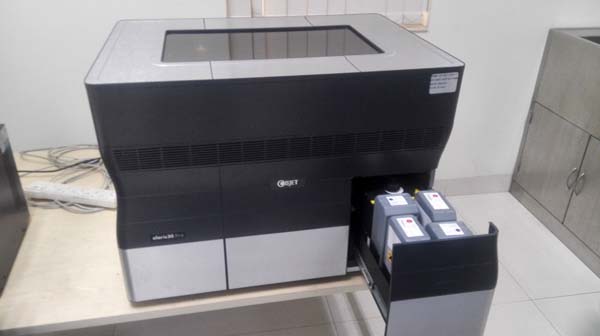
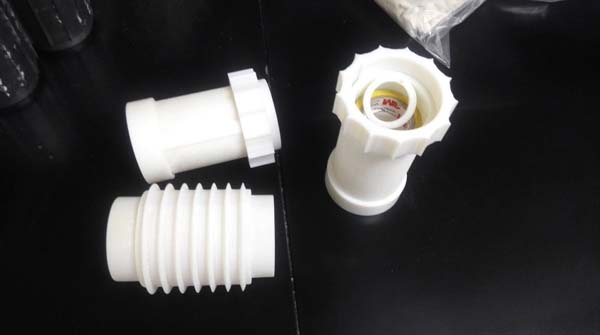
|
|
|
|
Cap & Thread Finishes: (GPI)
Screw thread cap sizes are expressed in two numbers, which refer to the cap diameter (in millimeters) & the GPI finish (at the top of the container). For example, a size 38-430 cap has a diameter of 38 mm, & fits a container with a 430 GPI thread finish. GPI refers to the ¡°Glass Packaging Institute¡± which is responsible for establishing & issuing uniform standards regarding the types of finishes produced by American Glass Manufactures. The cap industry has not standard on dimensions the way the glass industry has & it usually advantageous to buy both glass & cap from the same supplier whenever possible. Similar to the glass industry when cap finish is designated as 38-430, it means that the nominal diameter measured across the inside of the cap at the opening is approx. 38mm. The 430 designates a specific style of thread. The thread finish of the cap & glass must be the same. A glass with a 38-430 thread finish should be used with a cap that has a 38-430 thread finish. As a result the length of the cap may vary slightly from GPI¡¯s published values. Please review the charts. The dimensions are in inches.
Determining Cap¡¯s Thread Finish & Style:
To determine the cap size, place a ruler across the cap opening & read from one side of the inner wall to the opposite side of the inner wall. Compare this number to the numbers found in the ¡°T¡± dimension columns in the table above. Once this number is found in the table, follow the row to the far left to find the ¡°Nominal Diameter¡± of the cap. To determine the specific style of thread, measure the depth of the cap from the liner surface to the outside edge of the cap. Compare this to the numbers found in the ¡°H¡± dimension columns in the table above that appear in the same row as the Nominal Diameter of the cap. Once this number is found in the table, follow the column to the top to find the specific style number. The dimensions in the tables are approximate & will probably be slightly different from what is measured (especially the ¡°H¡± dimension-due to variations in liner thickness), but should be close enough to allow for proper determination of the cap size.
Suggested Torques for Caps:
The integrity of the cap to glass seal is dependent upon a number of variables, such as the materials of the cap, liner & glass, the sealing surface of the glass, & the application torque applied to the cap. The most important of these is the application torque. If the cap is applied too loosely, the contents could leak (especially during shipping). If the cap is applied too tightly, it may be too difficult to remove the cap, or the glass could break during application. The table below offers some suggested torques that should provide an adequate seal for most applications. It is recommended that proper tests be performed to determine the optimum torque for the application. The most practical way to check the tightness is to measure the removal torque after the cap has been on the glass for about 5 minutes. The removal torque should closely approximate the application torque. The minimum removal torque noted in the table should be maintained after a 24 hour period. Dimensions are in inch-pounds.
Polypropylene (PP) Caps:
Rigid, solid, durable in cap form. Opaque, natural grayish yellow in natural form and does come in a variety of colors. Excellent stress crack & impact resistance. Excellent moisture barrier, good oil & alcohol barrier, poor gas barrier properties. Good chemical resistance. Serializable with EtO or autoclaving.
Typical Properties of PP: (general guideline only)
Max. Useable Temp. ¡ãC: 135
Sterilization: Autoclave: Yes, Gas: yes, Dry Heat: no, Radiation: no, Disinfectants: yes
Specific Gravity: 0.90
Flexibility: rigid
Brittleness Temp. ¡ãC: 0
Tensile Strength, psi: 5000
H2O Adsorption/%: <0.02 |
|
|
|
Metal Closures
Metal closures offer the widest range of temperature tolerances and are very resistant to fracture from impact. A metal closure is manufactured from either steel (coated with anti-corrosive coating of either chromeplate or tinplate) or aluminum. |
|
|
|
Plastic Closures
There are two basic types of plastic closures used for scientific applications: thermoset and thermoplastic.
Thermoset closures cannot be remelted after they are formed. They provide the widest range of chemical compatibility and they exhibit the most tolerance to temperature of all plastic closures. Because thermoset closures are rigid, they provide the most consistent adherence to close dimensional tolerances. Common resins include urea, phenolic, and melamine.
Thermoplastic closures can be remelted after they are formed. They are known for good impact strength, cost effectiveness, and pliability. Common resins include polypropylene (autoclavable) and polyethylene. |
|
|
|
We are engaged in manufacturing, supplying and also exporting an exclusive array of Aluminum Screw Lid Tin, Aluaminum crimp on tin, Aluminum snap on tin, Aluminum window tin, Aluminum lip balm tin, Aluminum body butter tin. Aluminum cream tin for Cosmetics that has been made possible with the assistance of our skilled and highly diligent team. The range that we offer to the valued clients are manufactured with utmost precision and are made available at the most competitive price, because of which clients give importance to our products.
For more information, , you can review them on our website www.infullpak.com and email to us sales@infullpak.com if there is any item fine with you. |
|
|
|
Being a client centric organization, we are instrumental in offering Aluminum Screw Lid Tin to our valued patrons. Aluminium Screw Lid Tin, Aluminum Metal Screw Lid Tin and Aluminum Screw Lid Tin for Cosmetics are some of the products that come under our range of Aluminum Screw Lid Tin. This range of offered products have durable standards and are highly reliable besides these are made available at the most competitive and reasonable price. Our offered products are also demanded largely as these comply with organization set quality standards in an efficient manner.
Supported by our diligent team, we are actively engaged in manufacturing, supplying and exporting a reliable range of Aluminum Screw Lid Tin to our valued clients. This offered range of lid tins are manufactured and designed using finest quality aluminum procured from the most accredited source. Furthermore, quality controllers appointed by us are very skilled who test our products stringently so as to make sure that that is has no flaws.
You can review our alumimnum tins in different shape, design and sizes on our website www.infullpak.com and email to us if any one work for your product.
|
|
|
|
Key Difference: Aluminum foil is a thin sheet of aluminum that is less than 0.2 millimeters in thickness and can be used for various different things around the house. Tin foil is a thin sheet of foil made from tin. This was the most common type of packaging and insulating material used before the World War II, following which aluminum became the cheapest material and went into mass production.
Aluminum foils and tin foils are two different types of packaging materials, but tin foils have now become of obsolete. Aluminum foils have become the more common packaging due to it being widely available. Tin foils are less sturdy and stiffer compared to aluminum and can also leave a bitter taste in the food. The confusion between the two arises from the term tin foil now being used to refer to aluminum foil, because of the similarities between the two.
Aluminum FoilAluminum foil is a thin sheet of aluminum that is less than 0.2 millimeters in thickness and can be used for various different things around the house. Aluminum sheets vary in thickness depending on what the foil is supposed to be used for. The most common foil that are available for commercial use are 0.016 millimeters thick, while heavy duty household foil is typically 0.024 millimeters. Aluminum is mostly used for packaging foods and other materials. Aluminum at home is used to keep the air from the fridge to contaminate the smell of the food, while others are used to packing the item. Aluminum foils are easy to tear and are often used with other materials such as plastic or paper wraps to ensure more sturdiness.
In addition to packaging, aluminum is also used for thermal insulation, cables and electronics because of its ability to conduct electricity. Aluminum foil is made by rolling aluminum sheet ingots casts, which are then re-rolled multiple times until the desired thickness is achieved. The sheets are applied heat but are cold-rolled to ensure it does not tear apart. The press machine has a sensor attached passes beta radiation through the foil to check the thickness of the foil and accordingly changes the process to either make the sheet thicker or thinner. The sheet is also lubricated to ensure that it does not become marked with a herringbone pattern. The lubricants usually burned-off during the heating and rolling process. When the thickness of the sheet is less than 0.025 mm, two layers are usually put together for the final pass and are later separated. The two sheets when separated results in one side of the foil sheet being shiny, while the other being matte. Aluminum sheets are used for storage, packaging, cooking and for many other household purposes, making it a pretty useful sheet to have around the house.
Tin FoilTin foil is a thin sheet of foil made from tin. This was the most common type of packaging and insulating material used before the World War II, following which aluminum became the cheapest material and went into mass production. Tin foil is actually much expensive and less durable compared to aluminum foil. The term tin foil has actually stuck, with many people still referring to aluminum foil as tin foil in the US and the UK. This is mostly because of the similarities between the two in appearance.
In addition to tin foil, tin was also popular in cans. Tin foils were also used as a filling for tooth cavities before the 20th century. It was also used in recordings with the first audio recordings on phonograph cylinders were made on tin foil. These days, tin foils are used in electrical capacitors. Tin foils are made using a similar process to aluminum foils; the foil is rolled from a thin leaf of tin. Tin foils are actually stiffer than aluminum foil and can leave a bitter taste to food wrapped in it. Tin was replaced by aluminum in the 1910s, but the name tin foil is still widely used. |
|
|
|
Aluminum vs Tin
Tin is rarely found on Earth, as it is the 49th most abundant metal; whereas aluminum is the 3rd most abundant metal and the 9th most abundant element on Earth, found almost everywhere. Aluminum is silvery white to grey in color, whereas tin is silvery grey. The atomic number of tin is 50, with a symbol of Sn, and aluminum has the atomic number 13, with the symbol Al.
Tin has been used by humans since ancient times, when compared to aluminum which was discovered quite late in human history. Tin does not occur by itself, and is extracted from another compound; likewise, aluminum is also not found free in nature, but is combined with other elements in a dissolved state. Both form alloys ¨C tin forms an alloy with copper to make bronze, pewter and soft solder, and is used widely for coatings, such as for steel cans and sheets.
Tin has been in use for making jewelry and ornaments, whereas aluminum had once been considered as a rare metal, and more expensive than gold.
Aluminum and tin are both very pliable and flexible metals. They are both anti corrosive and easily machined. Tin, when compared to aluminum, has a crystalline structure. Aluminum and tin are non-ferrous metals, and make a variety of food and soda cans because both metals are ductile and inexpensive recyclable materials. Tin, when compared to steel, is more inexpensive.
Aluminum is often confused with tin, such as tin foil etc. Aluminum has replaced tin in industrial applications, such as for cans. Tin is considered to be toxic to humans, and so is aluminum, but not inherently toxic. It is believed that if they are both absorbed or inhaled by some humans, they can pose an ingestion risk, while aluminum is considered to be related with Alzheimer¡¯s disease.
They are both classified as poor metals, as they share extreme malleability properties. Both of the metals are extremely light weight. Aluminum is a good conductor of heat and energy when compared to tin, which is better than ceramic, etc, but not better than aluminum. Aluminum can be wired and used for manufacturing in industries such as aerospace, automobile, marine and others. Pure tin is too weak, so it is alloyed with other metals to make it stronger, whereas aluminum is a much stronger metal than tin.
Tin was used as an ordinary household material in the 1800¡¯s, particularly popular with the labor class. It was a low cost, gives a bright luster, and things made of iron or steel were dipped in molten tin. Tin items were also used as gifts by the majority of people in the olden days, especially for the tenth anniversary, also known as the ¡®tin anniversary¡¯. Tin is considered to be a good replacement for other harmful metals, such as mercury, lead or cadmium; whereas aluminum is currently replacing tin. The melting point of tin happens at a low temperature, and it is highly fluid when molten with a higher boiling point. Aluminum plays no, or very little biological role; likewise, tin seems to have no significant role for humans.
Summary:
1. Tin is cheaper than aluminum, but aluminum is replacing tin.
2. Aluminum is stronger and used for industrial purposes and for other industries, such as aerospace or automobiles.
3. Tin is most commonly used for plating steel sheets.
4. Aluminum is more abundant in nature when compared to tin.
5. Tin is weaker compared to aluminum, which is much stronger and more lightweight than tin. |
|
|
|
Aluminum or Tin?
One question I get asked often is ¡°what¡¯s the difference between tin cans and aluminum cans?¡±. In fact, I often hear people using the terms as if they¡¯re interchangeable. Tin cans are usually used in packaging food like soup, vegetables, and Spaghetti O¡¯s, while aluminum cans are usually used for beverages like soda or beer. There are always exceptions of course. For example, tuna fish and pet foods often come in aluminum containers while fruit juices and punch often come in large tin cans. The easiest way to tell the difference is to use a magnet. Tin cans are made of steel and will stick to a magnet. Aluminum cans are not affected by magnetic forces. If you¡¯re selling your cans for recycling you want to keep the two kinds seperate. If you don¡¯t have a magnet, drop by our office and ask the cashier for a complimentary one. |
|
|
|
 
Child-resistant packaging is now common for medications. There are a variety of methods to secure medications, including caps that must be pinched or pushed down while turning. It may be required by regulation for prescription drugs, for over the counter medications, for pesticides, or for household chemicals where there is a significant risk of death from ingestion.
Patients can request medications come in non-protected bottles at their pharmacy, but this is not recommended for patients with young children in the home.] Because some children will defeat child-resistant caps, medicine should always be stored up out of reach in latched cabinets or closets. |
|
|
|
 
RingCrown (also known as RipCap, Ring-pull closure or pull off caps) is a bottle closure that can be opened without any tools. It has a ring that can be pulled and therefore detach the cap from a bottle. The cap splits along scores in the cap so it loosens from the bottle and is removed. Drink companies use ring pull caps to differentiate from competitors.
History of RingCrown
"ALKA", the predecessor of modern ring-pull caps were introduced during the 1930s. ALKA had a seal made of natural cork. It became popular in Nordic countries as an easy-to-open cap. Alka made of aluminum had a tab that is pulled to remove the cap. There is no scoring on an ALKA cap. In the 1970s the MaxiCap was first produced. A MaxiCap is an aluminum closure with scoring and a tab to pull. They were easier to use than the ALKA and pre-manufactured outside of the bottling plant. This allowed for increased production speeds on the bottling line. Soon after the MaxiCap, came the RingCrown closure. Invented in the early 1980s originally called MaxiCrown and later known as RingCrown. RingCrown is easier to use than its predecessors, it has an attached ring rather than static pull off tab.
|
|
|
|
 
Screw on closures are the most common bottle caps. They are easy to apply by a wide variety of automated equipment, or they can be applied by hand. The application torque of closures however must be controlled in order for the closures to perform properly in the field. Closures must be applied tight enough to maintain a seal and to resist closure back-off, but must be not be applied so tightly that the end user cannot remove the closure. They are often found on top of beers, such as Coors or Dos Equis.
Screw caps were originally an internal thread design. A glass bottle / jar with an internal screw-thread immediately below a gasket-seat, having a beveled seat, was patented by Hyman (Himan) Frank of the William Frank & Sons, Inc. of Pittsburgh, PA. He was awarded patent US 130208 A on August 6, 1872.
|
|
|
|
Foamed polyethylene (F217) Commonly used with plastic screw caps. F-217 is a soft polyethylene foam core covered on top and bottom with solid, clear polyethylene supplied in 0.050 inch thickness. F217 has become the industry standard due to its all purpose compatibility, resilient, compressible seal, cleanliness (no pulp dust) and economy. F217 liners have excellent chemical resistance and a low moisture transmission rate. F217 has good taste and odor resistance.
Plastiso Plastisol is the standard lining material used in metal closures for vacuum packing glass bottles and jars. Plastisol is a flowed-in compound, usually a dispersion of PVC resins in plasticizers. It forms a solid, self-bonding, sealing gasket in the closures. Plastisol liners are used in metal twist-off and metal continuous thread screw caps for use on hot-pack food products where the preservation of a vacuum is essential.
Pressure-sensitive liners Styrene foam material coated on the down facing side with torque-activated adhesive. Pressure-sensitive inner seals adhere to plastic or glass bottles with normal application torque. Pressures sensitive liners are supplied pressed into closures and adhere to the bottle finish when the closure is applied. Pressure-sensitive liners stick to the container because one side is coated with pockets of adhesive. When the closure is applied to the container, the pockets of adhesive rupture between the closure and finish of bottle or jar. The pressure-sensitive liners then stick to the bottle or jar and remain in place when the closure is removed. No extra equipment is required. The closures are supplied with a standard liner as a backing. This material needs a dry land area on the bottle and therefore is suitable only for use with dry products such as vitamins, foods and pharmaceuticals.
Polyseal cone liners Molded in Low Density Polyethylene, Polyseal cone liners form to the inside of the bottle neck providing a leakproof seal which guards against back-off and product evaporation. Excellent for use with acid products and essential oils, these closures are recommended for use on glass bottles only. |
|
|
|
Plastic bottle screw cap used to seal a plastic bottle.
Glass stoppers for wine bottles and a cork stopper. A "sports cap" made of plastic, as seen on many water bottles, here seen in closed configuration. Same sports cap in open mode, allowing the liquid to pass around the central blue piece. A recloseable wire, ceramic, and rubber bottle clasp, from a German mineral water bottle.
|
|
|
|
The crown cork was patented by William Painter on February 2, 1892 (U.S. Patent 468,258). It had 24 teeth[citation needed] and a cork seal with a paper backing to prevent contact between the contents and the metal cap. The current version has 21 teeth. To open these bottles, a bottle opener is generally used.
The height of the crown cap was reduced and specified in the German standard DIN 6099 in the 1960s. This also defined the "twist-off" crown cap, now used in the United States, Canada, and Australia. This cap is pressed around screw threads instead of a flange, and can be removed by twisting the cap by hand, eliminating the need for an opener.
|
|
|
|
 A bottle cap seals the top opening of a bottle. A cap is typically colorfully decorated with the logo of the brand of beverage. Plastic caps are used for plastic bottles, while metal with plastic backing is used for glass; the metal is usually steel.[citation needed] Plastic caps may have a pour spout. Flip-Top caps like Flapper closures provide controlled dispensing of dry products. Caps for plastic bottles are often made of a different type of plastic than the bottle.
|
|
|
|
Plastic PET/PETE Bottles
PET/PETE bottles are made of Polyethylene terephthalate plastic, which is ideal for storing liquid, creams or gel. This is composed of tough thermoplastic polymer resin and is a popular choice for storing cosmetics.
This type of container is easy to produce and is very cost efficient. This is sometimes used with synthetic fibers and glass fibers in order to create a tougher container.
Uses for PET/PETE Bottles: PET/PETE plastic bottles are used for storing liquid cosmetics such as lotions, soap or gels. They come in a variety of shapes and sizes, which make them the ideal packaging choice. The tough resin outer shell of these bottles can withstand humidity which helps the plastic act as a good moisture barrier, keeping the cosmetic liquid sealed inside.
Benefits of PET/PETE Bottles: This type of plastic container is very affordable. It is more cost efficient as compared to PP plastic, acrylic plastic and glass containers. PET/PETE bottles can be easily mass produced in just a matter of days. These are also very light-weight, which make them convenient to store or carry in a bag or purse.
Styles of PET/PETE Bottles PET/PETE plastic containers can be shaped into different styles. They usually come in cylinder bottles, however they can also be square shaped, triangular or heart shaped. The shape of the bottle depends on the attachment needed and the liquid to be stored inside. These can be molded using the one-step or two-step process, depending on the complexity of the shape and bottle
requirements.
Sizes of PET/PETE Bottles These bottles come in different sizes to suit the liquid to be stored. They can come in sizes as small as 0.5 fl oz and as large as 35 lf oz. This depends on the cosmetic liquid that will be placed inside the bottle. Usually, liquid primers and other make-up cosmetics require small bottles, lotion or hair spray will have to be stored in larger PET/PETE bottles.
Colors o PET/PETE Bottles: PET/PETE plastics can be pre-colored or tinted. They are usually clear or transparent, however they can also be tinted, frosted or powder coated. Some PET bottles are coated with an aluminium sheet in order to create a metallic and elegant effect. These types of bottles can also take on a gradient effect.
Designs of PET/PETE Bottles: The cosmetic packaging of bottles made of this material is easy to execute. The bottles can either have a sticker label or they can go through a silk screen process where the label is directly placed on the body of the bottle. Unlike acrylic plastic or glass bottles, PET/PETE bottles cannot have an embossed design.
Accessory for PET/PETE Bottles
PET/PETE bottles are the most common containers used for lotions and hair spray. They can be fitted with lotion pumps or finger sprayers for easy dispensing. These attachments need to fit the neck or opening of the bottle so that there is no leakage. Non-screw caps which can be attached to these containers are spill proof and ideal for mist or hair sprays, however they are not reusable or refillable. If the cosmetic inside the bottle can be poured for application, a simple screw or pop cap can be used.
|
|
|
|
Loose Powder Containers and Jar
There is an art to creating cosmetic packaging. The best products will offer packaging that combines both form and function. When it comes to loose powder packaging, some companies are hitting the nail on the head while a surprising number (including some big name brands) are missing the mark. Creating a loose powder container that customers love will help a beauty brand to sell more product and keep customers coming back.
Loose Powder Container Basics The purpose of loose powder containers is to allow users to pick up the product with a large powder brush. For this reason, the best containers are simple shapes and have a large opening to allow for the size of the brush.
The containers should have tight fitting lids to prevent the product from spilling. With loose powders, any lost product will quickly lead to a huge mess.
Adding Sifters Some brands choose to use an open container for their loose powders. This can be helpful for getting a good amount of product on the brush, but the majority of users do not prefer an open container. The reason is simple, an open container means that you will, inevitably, spill the product. To a consumer, lost product means lost money. In fact, many individuals will choose to transfer product from open containers into more manageable containers after purchasing the product.
To make a container usable, a sifter is not only recommended but perhaps even necessary. A sifter allows the user to turn the container upside down, with the lid on, to free a small amount of the product. It gives the user control over how much product is released. This prevents too much product from getting onto the brush at one time. It also means that if the container is dropped or moved, the amount of product spilled will be minimal.
A Container Made to Travel One of the big complaints with loose powder containers is that the product creates a huge mess when the container is transported. For those who travel frequently or even move their makeup cases from room to room, this is a huge issue. There¡¯s nothing worse than traveling, opening your makeup bag, and finding spilled product covering everything. When designing a loose powder container, it¡¯s important to ensure that the powder will be contained regardless of how much the container is moved.
A Locking Sifter The solution to the issue of leaked powder is to include a lock option on the sifter. Manufacturers have already discovered the need for sifters to provide a limited amount of product at a time. This is a great first step toward creating the perfect container. However, when the container is flipped, turned, and jostled, sifters will allow a large amount of product to escape. This is what causes the mess when the product is opened later. A locking feature simply allows the user to turn the sifter off by covering the holes or to turn on the sifter by opening them back up. This may seem like a small detail, but it makes all
the difference in saving product and sanity for the consumer.
|
|
|
|
Roll-on bottles are really convenient and handy bottles that hold fragrances or perfumes. Roll-on bottles used to be the premiere method of storing and holding perfumes for many, many years. Many manufacturers now choose to use the spray bottle instead of roll-on bottles but there are still tremendous benefits associated with the roll-on bottle as a method of storage, for both functionality and application. A roll-on bottle is generally a smaller sized bottle that has a circular ball at the top, that when rolled against or on something, the contents of the bottle, come out. A small twist cap is usually attached on top of the circular ball to keep it clean and pristine.
The great thing about roll-on bottles is that their method of use is completely different than that of the spray bottle. Many perfume sprays that come out in a mist, distribute too much of the fragrance around. When using a roll-on bottle to apply perfume or a fragrance, the roll on spout puts a designated amount of fragrance on the selected area. It¡¯s more localized and it¡¯s also a more potent method of application. It is said that applying fragrance this way is actually better and helps the fragrance last longer. A roll-on bottle is usually small, it¡¯s handy, and it can be carried in a purse or in a pocket. It¡¯s much more travel friendly than entire bottles of perfume.
Roll-on bottles come in many different colors and designs. Depending on the need or look that is trying to be achieved. There are plain glass bottles, there are some that come in colors. Different hues such as red, blue, green and even frosted. The frosted roll-on bottles are pretty cool because they look much like an antique or something that was specially crafted and unique.
Also, some bottles come in the hues of bronze and silver for a more stylish, up scale look. A cool thing about some of these bottles that have been designed lately, is that they have a bit more flare and interesting nuances, than the old bottles did. Some bottles can even be purchased with a specific swirl or encrusted design. This adds a little bit of luxury and authenticity to the bottles. Having choices is so important, so whether it¡¯s a clear bottle, a silver one or an encrusted one it¡¯s something that will be both convenient and cool.
Lastly, roll-on bottles aren¡¯t all tube like and circular. There are actually bottles that come in rectangular or octagonal shapes for those who want a different look and feel to their bottles, but still want the same application and convenience that the roll-on bottles give. There is no shortage of options when it comes to these type of bottles. They are great because the method of application that is used is very different than the standard perfume bottle and many would say, much better. Add to that the functionality as well as size of these bottles, they can be carried around in mostly anything, a bag, a briefcase, the car, a pocket. There is no limit to the amount of places these little, handy bottles can be carried. These bottles are without a doubt, a great way to package and store fragrance.
|
|
|