|
Polypropylene (PP), also known as polypropene, is a thermoplastic polymer used in a wide variety of applications including packaging and labeling, textiles (e.g., ropes, thermal underwear and carpets), stationery, plastic parts and reusable containers of various types, laboratory equipment, loudspeakers, automotive components, and polymer banknotes. An addition polymer made from the monomer propylene, it is rugged and unusually resistant to many chemical solvents, bases and acids.
Polypropylene has a relatively slippery "low energy surface" that means that many common glues will not form adequate joints. Joining of polypropylene is often done using welding processes.
The melting point of polypropylene occurs at a range, so a melting point is determined by finding the highest temperature of a differential scanning calorimetry chart. Perfectly isotactic PP has a melting point of 171 ¡ãC (340 ¡ãF). Commercial isotactic PP has a melting point that ranges from 160 to 166 ¡ãC (320 to 331 ¡ãF), depending on atactic material and crystallinity. Syndiotactic PP with a crystallinity of 30% has a melting point of 130 ¡ãC (266 ¡ãF). Below 0 ¡ãC, PP becomes brittle.
The thermal expansion of polypropylene is very large, but somewhat less than that of polyethylene.
Polypropylene is recyclable and has the number "5" as its resin identification code. |
|
|
|
How a foam pump work?
A foam pump emits doses of the liquid contained in the bottle in the form of foam. Foam is created in the foamer chamber. The liquid constituents are mixed in the foaming chamber and this is discharged through a nylon mesh. The neck finish size of a foam pump is bigger than the neck finish size of other types of pumps, to accommodate the foamer chamber. The usual neck size of a foam pump is 40 or 43mm.
Where hair-coloring products previously contained instructions to vigorously shake the product, squeeze the bottle, and turn upside-down to disperse the product, foamers do not require any such actions.[citation needed] Some foaming dispensers include suction on the bottom to allow the container to remain upright. |
|
|
|
A foam pump, or squeeze foamer and dispensing device is a non-aerosol way of dispensing liquid materials. The foam pump outputs the liquid in the form of foam and it is operated by squeezing. The parts of the foam pump are similar to those of the other pump devices. Many times the foaming pump comes with a protective cap. Most of the components are made from polypropylene (PP).
Foamers can be purchased alone, or filled with a liquid product like soap. When the liquid is mixed with air, the liquid product can be dispersed through the pump-top as a foam. Foamers can also be re-used with different liquid products to extend the mass of the liquid by creating a foam-version. |
|
|
|
What is a Jug
A jug is a type of container commonly used to hold liquid. It has an opening, often narrow, from which to pour or drink, and often has a handle. Most jugs throughout history have been made of ceramic, glass or plastic. Some Native American and other tribes created liquid holding vessels by making woven baskets lined with an asphaltum sealer
In American English usage, a jug is a large container with a narrow mouth and handle for liquids, and may be used to describe thin plastic sealed shop packaging for milk and other liquids. In all other English speaking countries a jug is any container with a handle and a mouth and spout for liquid, and not used for retail packaging. In American English "pitcher" is the usual word for wide-mouthed vessels, but all other English speaking countries these are called "jugs".
Plastic Jug is a large, deep Plastic container with a narrow opening and a handle which is used for liquid laundry detergent , cleanser or Sauces, Milk packaging. |
|
|
|
Plastic Jars - Polystyrene (PS)
Plastic jars made from styrene offer excellent clarity and stiffness at an economical cost. These jars are commonly used with dry products including vitamins, petroleum jellies, and Nut fruits. Styrene does not provide good barrier properties, and exhibits poor impact resistance. |
|
|
|
Plastic Jars Or Bottles - Polypropylene (PP)
Plastic jars made from polypropylene provide a rigid package with an excellent moisture barrier.
One major advantage of polypropylene is its stability at high temperatures, up to 200¡ã F. Polypropylene bottles and jars are autoclavable and offer the potential for steam sterilization. The compatibility of PP with high filling temperatures is responsible for its use with hot fill products such as pancake syrup.
PP bottles have excellent chemical resistance, but provide poor impact resistance in cold temperatures |
|
|
|
Plastic Bottles - Polyvinyl Chloride (PVC)
Plastic Bottles made PVC are naturally clear, have extremely good resistance to oils, and have very low oxygen transmission. PVC bottles provide an excellent barrier to most gases and drop impact resistance is also very good. This material is chemically resistant, but it is vulnerable to solvents.
PVC bottles are an excellent choice for salad oil, mineral oil, and vinegar. It is also commonly used for shampoos and cosmetic products. PVC exhibits poor resistance to high temperatures and will distort at 160¡ã F, making it incompatible with hot filled products |
|
|
|
Plastic PET Bottles - PET/PETE/ Polyethylene Terephthalate
Plastic Bottles made from Polyethylene Terephthalate are commonly used for carbonated beverage bottles. PET provides very good alcohol and essential oil barrier properties, generally good chemical resistance (although acetones and ketones will attack PET) and a high degree of impact resistance and tensile strength. The orienting process serves to improve gas and moisture barrier properties and impact strength.This material does not provide resistance to high temperature applications -- max. temp. 160¡ã F.
|
|
|
|
Plastic Bottles - Low Density Polyethylene (LDPE)
LDPE is similar to HDPE in composition. It is less rigid and generally less chemically resistant than HDPE, but is more translucent. LDPE is used primarily for squeeze applications. LDPE is significantly more expensive than HDPE |
|
|
|
Plastic Bottles - High Density Polyethylene (HDPE)
HDPE is the most widely used resin for plastic bottles. This material is economical, impact resistant, and provides a good moisture barrier. HDPE is compatible with a wide range of products including acids and caustics but is not compatible with solvents. It is supplied in FDA approved food grade.
Plastic Bottles made from HDPE are naturally translucent and flexible. The addition of color will make HDPE bottles opaque although not glossy. HDPE plastic bottles lend themselves readily to silk screen decoration.
While HDPE bottles provide good protection at below freezing temperatures, they cannot be used with products filled at over 160¡ã F or products requiring a hermetic (vacuum) seal. HDPE is NOT suitable for use with essential oils. |
|
|
|
A Mason jar, named after John Landis Mason who first invented and patented it in 1858, is a molded glass jar used in home canning to preserve food. The jar's mouth has a screw thread on its outer perimeter to accept a metal ring (or "band"). The band, when screwed down, presses a separate stamped steel disc-shaped lid against the jar's rim. An integral rubber ring on the underside of the lid creates a hermetic seal. The bands and lids usually come with new jars, but they are also sold separately. While the bands are reusable, the lids are intended for single use when canning. Largely supplanted by other products and methods for commercial canning, such as tin cans and plastic containers, glass jars and metal lids are still commonly used in home canning. Mason jars are also called Ball jars, in reference to the Ball Corporation, an early and prolific manufacturer of glass canning jars; fruit jars for a common content; and glass canning jars a generic term reflecting their material. Lightning fruit jars, another type of Mason jar, was not as common as the screw-thread version, but they were popular for home canning in the late nineteenth and early twentieth centuries.
|
|
|
|
PET is polyethylene terephthalate. It's a plastic resin and the most common type of polyester. Two monomers¡ªmodified ethylene glycol and purified terephthalic acid¡ªare combined to form the polymer called polyethylene terephthalate. PET was discovered and patented in England in 1941.
PET is the plastic labeled with the #1 code. Many beverages, food items and other consumer products are delivered in bottles or packages made from PET. The #1 code is usually found on or near the bottom of the container.
PET makes good packages for food and non-food items. Manufacturers like it because it's safe, strong, transparent and versatile. Customers choose it for its safety, light weight, resealability, shatter-resistance and recyclability. Up to 100% of a PET package can be made from recycled PET, and the material can be recycled again and again.
PET can be recycled into many new products. It's used to make new bottles, but recycled PET can also be made into fiber for carpets; fabric for t-shirts or fleece jackets; fiberfill for sleeping bags, winter coats, and dog beds; industrial strapping; sheet and thermoformed (clam shell) packaging; and automotive parts such as headliners, bumpers, and door panels.
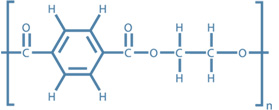
|
|
|
|
Dentification code number For PET Bottes and PET Jars
Bottles made of polyethylene terephthalate (PET, sometimes PETE) can be "recycled" to reuse the material out of which they are made and to reduce the amount of waste going into landfills. PET is semiporous and absorbs molecules of the food or beverage contained, and the residue is difficult to remove: Heating the plastic enough for sterilization would destroy it. Therefore, most recycled bottles are used to make lower grade products, such as carpets.[citation needed] To make a food grade plastic, the bottles need to be hydrolysed down to monomers, which are purified and then re-polymerised to make new PET. In many countries, PET plastics are coded with the resin identification code number "1" inside the universal recycling symbol, usually located on the bottom of the container. |
|
|
|
Cap & Thread Finishes: (GPI)
Screw thread cap sizes are expressed in two numbers, which refer to the cap diameter (in millimeters) & the GPI finish (at the top of the container). For example, a size 38-430 cap has a diameter of 38 mm, & fits a container with a 430 GPI thread finish. GPI refers to the ¡°Glass Packaging Institute¡± which is responsible for establishing & issuing uniform standards regarding the types of finishes produced by American Glass Manufactures. The cap industry has not standard on dimensions the way the glass industry has & it usually advantageous to buy both glass & cap from the same supplier whenever possible. Similar to the glass industry when cap finish is designated as 38-430, it means that the nominal diameter measured across the inside of the cap at the opening is approx. 38mm. The 430 designates a specific style of thread. The thread finish of the cap & glass must be the same. A glass with a 38-430 thread finish should be used with a cap that has a 38-430 thread finish. As a result the length of the cap may vary slightly from GPI¡¯s published values. Please review the charts. The dimensions are in inches.
Determining Cap¡¯s Thread Finish & Style:
To determine the cap size, place a ruler across the cap opening & read from one side of the inner wall to the opposite side of the inner wall. Compare this number to the numbers found in the ¡°T¡± dimension columns in the table above. Once this number is found in the table, follow the row to the far left to find the ¡°Nominal Diameter¡± of the cap. To determine the specific style of thread, measure the depth of the cap from the liner surface to the outside edge of the cap. Compare this to the numbers found in the ¡°H¡± dimension columns in the table above that appear in the same row as the Nominal Diameter of the cap. Once this number is found in the table, follow the column to the top to find the specific style number. The dimensions in the tables are approximate & will probably be slightly different from what is measured (especially the ¡°H¡± dimension-due to variations in liner thickness), but should be close enough to allow for proper determination of the cap size.
Suggested Torques for Caps:
The integrity of the cap to glass seal is dependent upon a number of variables, such as the materials of the cap, liner & glass, the sealing surface of the glass, & the application torque applied to the cap. The most important of these is the application torque. If the cap is applied too loosely, the contents could leak (especially during shipping). If the cap is applied too tightly, it may be too difficult to remove the cap, or the glass could break during application. The table below offers some suggested torques that should provide an adequate seal for most applications. It is recommended that proper tests be performed to determine the optimum torque for the application. The most practical way to check the tightness is to measure the removal torque after the cap has been on the glass for about 5 minutes. The removal torque should closely approximate the application torque. The minimum removal torque noted in the table should be maintained after a 24 hour period. Dimensions are in inch-pounds.
Polypropylene (PP) Caps:
Rigid, solid, durable in cap form. Opaque, natural grayish yellow in natural form and does come in a variety of colors. Excellent stress crack & impact resistance. Excellent moisture barrier, good oil & alcohol barrier, poor gas barrier properties. Good chemical resistance. Serializable with EtO or autoclaving.
Typical Properties of PP: (general guideline only)
Max. Useable Temp. ¡ãC: 135
Sterilization: Autoclave: Yes, Gas: yes, Dry Heat: no, Radiation: no, Disinfectants: yes
Specific Gravity: 0.90
Flexibility: rigid
Brittleness Temp. ¡ãC: 0
Tensile Strength, psi: 5000
H2O Adsorption/%: <0.02 |
|
|
|
Metal Closures
Metal closures offer the widest range of temperature tolerances and are very resistant to fracture from impact. A metal closure is manufactured from either steel (coated with anti-corrosive coating of either chromeplate or tinplate) or aluminum. |
|
|
|
Plastic Closures
There are two basic types of plastic closures used for scientific applications: thermoset and thermoplastic.
Thermoset closures cannot be remelted after they are formed. They provide the widest range of chemical compatibility and they exhibit the most tolerance to temperature of all plastic closures. Because thermoset closures are rigid, they provide the most consistent adherence to close dimensional tolerances. Common resins include urea, phenolic, and melamine.
Thermoplastic closures can be remelted after they are formed. They are known for good impact strength, cost effectiveness, and pliability. Common resins include polypropylene (autoclavable) and polyethylene. |
|
|
|
Key Difference: Aluminum foil is a thin sheet of aluminum that is less than 0.2 millimeters in thickness and can be used for various different things around the house. Tin foil is a thin sheet of foil made from tin. This was the most common type of packaging and insulating material used before the World War II, following which aluminum became the cheapest material and went into mass production.
Aluminum foils and tin foils are two different types of packaging materials, but tin foils have now become of obsolete. Aluminum foils have become the more common packaging due to it being widely available. Tin foils are less sturdy and stiffer compared to aluminum and can also leave a bitter taste in the food. The confusion between the two arises from the term tin foil now being used to refer to aluminum foil, because of the similarities between the two.
Aluminum FoilAluminum foil is a thin sheet of aluminum that is less than 0.2 millimeters in thickness and can be used for various different things around the house. Aluminum sheets vary in thickness depending on what the foil is supposed to be used for. The most common foil that are available for commercial use are 0.016 millimeters thick, while heavy duty household foil is typically 0.024 millimeters. Aluminum is mostly used for packaging foods and other materials. Aluminum at home is used to keep the air from the fridge to contaminate the smell of the food, while others are used to packing the item. Aluminum foils are easy to tear and are often used with other materials such as plastic or paper wraps to ensure more sturdiness.
In addition to packaging, aluminum is also used for thermal insulation, cables and electronics because of its ability to conduct electricity. Aluminum foil is made by rolling aluminum sheet ingots casts, which are then re-rolled multiple times until the desired thickness is achieved. The sheets are applied heat but are cold-rolled to ensure it does not tear apart. The press machine has a sensor attached passes beta radiation through the foil to check the thickness of the foil and accordingly changes the process to either make the sheet thicker or thinner. The sheet is also lubricated to ensure that it does not become marked with a herringbone pattern. The lubricants usually burned-off during the heating and rolling process. When the thickness of the sheet is less than 0.025 mm, two layers are usually put together for the final pass and are later separated. The two sheets when separated results in one side of the foil sheet being shiny, while the other being matte. Aluminum sheets are used for storage, packaging, cooking and for many other household purposes, making it a pretty useful sheet to have around the house.
Tin FoilTin foil is a thin sheet of foil made from tin. This was the most common type of packaging and insulating material used before the World War II, following which aluminum became the cheapest material and went into mass production. Tin foil is actually much expensive and less durable compared to aluminum foil. The term tin foil has actually stuck, with many people still referring to aluminum foil as tin foil in the US and the UK. This is mostly because of the similarities between the two in appearance.
In addition to tin foil, tin was also popular in cans. Tin foils were also used as a filling for tooth cavities before the 20th century. It was also used in recordings with the first audio recordings on phonograph cylinders were made on tin foil. These days, tin foils are used in electrical capacitors. Tin foils are made using a similar process to aluminum foils; the foil is rolled from a thin leaf of tin. Tin foils are actually stiffer than aluminum foil and can leave a bitter taste to food wrapped in it. Tin was replaced by aluminum in the 1910s, but the name tin foil is still widely used. |
|
|
|
Aluminum or Tin?
One question I get asked often is ¡°what¡¯s the difference between tin cans and aluminum cans?¡±. In fact, I often hear people using the terms as if they¡¯re interchangeable. Tin cans are usually used in packaging food like soup, vegetables, and Spaghetti O¡¯s, while aluminum cans are usually used for beverages like soda or beer. There are always exceptions of course. For example, tuna fish and pet foods often come in aluminum containers while fruit juices and punch often come in large tin cans. The easiest way to tell the difference is to use a magnet. Tin cans are made of steel and will stick to a magnet. Aluminum cans are not affected by magnetic forces. If you¡¯re selling your cans for recycling you want to keep the two kinds seperate. If you don¡¯t have a magnet, drop by our office and ask the cashier for a complimentary one. |
|
|
|
Plastic PET/PETE Bottles
PET/PETE bottles are made of Polyethylene terephthalate plastic, which is ideal for storing liquid, creams or gel. This is composed of tough thermoplastic polymer resin and is a popular choice for storing cosmetics.
This type of container is easy to produce and is very cost efficient. This is sometimes used with synthetic fibers and glass fibers in order to create a tougher container.
Uses for PET/PETE Bottles: PET/PETE plastic bottles are used for storing liquid cosmetics such as lotions, soap or gels. They come in a variety of shapes and sizes, which make them the ideal packaging choice. The tough resin outer shell of these bottles can withstand humidity which helps the plastic act as a good moisture barrier, keeping the cosmetic liquid sealed inside.
Benefits of PET/PETE Bottles: This type of plastic container is very affordable. It is more cost efficient as compared to PP plastic, acrylic plastic and glass containers. PET/PETE bottles can be easily mass produced in just a matter of days. These are also very light-weight, which make them convenient to store or carry in a bag or purse.
Styles of PET/PETE Bottles PET/PETE plastic containers can be shaped into different styles. They usually come in cylinder bottles, however they can also be square shaped, triangular or heart shaped. The shape of the bottle depends on the attachment needed and the liquid to be stored inside. These can be molded using the one-step or two-step process, depending on the complexity of the shape and bottle
requirements.
Sizes of PET/PETE Bottles These bottles come in different sizes to suit the liquid to be stored. They can come in sizes as small as 0.5 fl oz and as large as 35 lf oz. This depends on the cosmetic liquid that will be placed inside the bottle. Usually, liquid primers and other make-up cosmetics require small bottles, lotion or hair spray will have to be stored in larger PET/PETE bottles.
Colors o PET/PETE Bottles: PET/PETE plastics can be pre-colored or tinted. They are usually clear or transparent, however they can also be tinted, frosted or powder coated. Some PET bottles are coated with an aluminium sheet in order to create a metallic and elegant effect. These types of bottles can also take on a gradient effect.
Designs of PET/PETE Bottles: The cosmetic packaging of bottles made of this material is easy to execute. The bottles can either have a sticker label or they can go through a silk screen process where the label is directly placed on the body of the bottle. Unlike acrylic plastic or glass bottles, PET/PETE bottles cannot have an embossed design.
Accessory for PET/PETE Bottles
PET/PETE bottles are the most common containers used for lotions and hair spray. They can be fitted with lotion pumps or finger sprayers for easy dispensing. These attachments need to fit the neck or opening of the bottle so that there is no leakage. Non-screw caps which can be attached to these containers are spill proof and ideal for mist or hair sprays, however they are not reusable or refillable. If the cosmetic inside the bottle can be poured for application, a simple screw or pop cap can be used.
|
|
|
|
Roll-on bottles are really convenient and handy bottles that hold fragrances or perfumes. Roll-on bottles used to be the premiere method of storing and holding perfumes for many, many years. Many manufacturers now choose to use the spray bottle instead of roll-on bottles but there are still tremendous benefits associated with the roll-on bottle as a method of storage, for both functionality and application. A roll-on bottle is generally a smaller sized bottle that has a circular ball at the top, that when rolled against or on something, the contents of the bottle, come out. A small twist cap is usually attached on top of the circular ball to keep it clean and pristine.
The great thing about roll-on bottles is that their method of use is completely different than that of the spray bottle. Many perfume sprays that come out in a mist, distribute too much of the fragrance around. When using a roll-on bottle to apply perfume or a fragrance, the roll on spout puts a designated amount of fragrance on the selected area. It¡¯s more localized and it¡¯s also a more potent method of application. It is said that applying fragrance this way is actually better and helps the fragrance last longer. A roll-on bottle is usually small, it¡¯s handy, and it can be carried in a purse or in a pocket. It¡¯s much more travel friendly than entire bottles of perfume.
Roll-on bottles come in many different colors and designs. Depending on the need or look that is trying to be achieved. There are plain glass bottles, there are some that come in colors. Different hues such as red, blue, green and even frosted. The frosted roll-on bottles are pretty cool because they look much like an antique or something that was specially crafted and unique.
Also, some bottles come in the hues of bronze and silver for a more stylish, up scale look. A cool thing about some of these bottles that have been designed lately, is that they have a bit more flare and interesting nuances, than the old bottles did. Some bottles can even be purchased with a specific swirl or encrusted design. This adds a little bit of luxury and authenticity to the bottles. Having choices is so important, so whether it¡¯s a clear bottle, a silver one or an encrusted one it¡¯s something that will be both convenient and cool.
Lastly, roll-on bottles aren¡¯t all tube like and circular. There are actually bottles that come in rectangular or octagonal shapes for those who want a different look and feel to their bottles, but still want the same application and convenience that the roll-on bottles give. There is no shortage of options when it comes to these type of bottles. They are great because the method of application that is used is very different than the standard perfume bottle and many would say, much better. Add to that the functionality as well as size of these bottles, they can be carried around in mostly anything, a bag, a briefcase, the car, a pocket. There is no limit to the amount of places these little, handy bottles can be carried. These bottles are without a doubt, a great way to package and store fragrance.
|
|
|