|
在选择注塑机的规格型号之前,首先要査看注塑机生产厂家提供的产品说明书中的注塑机性能参数值。这些参数值是表示该注塑机的主要性能特征,根据所要生产塑料制品的一些技术要求[如制品用原料种类、牌号、制品的质(重)量及外形尺寸等]去查找说明书中与其相接近的参数值,这些参数值所对应的注塑机型号就是我们要选购的注塑机型号。 规格型号中重点要对照的数据,是制品的质(重)量(或容积)和外形尺寸与参数值的比例关系。即塑料制品的质(重)量与注塑机理论注射量(或容积)之间的比例要求,制品的长度尺寸及成型模具厚度尺寸之和与注塑机移动模板行程距离之间的尺寸要求条件。 |
|
|
|
在注塑成型塑料制品的生产过程中,螺杆(柱塞)前移时对塑化均匀熔料施加的推力,即为注射压力。施加的这个压力是为了克服熔料进人成型模具腔过程中,克服流经喷嘴、浇道和模具腔内各部位的摩擦阻力,保证熔料在此压力作用下充满型腔各部位。注射压力计算公式为
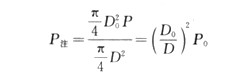
式中 P0——油压,MPa; D0——注射油缸内径,cm; D——螺杆(柱塞)外径,cm。 注射压力的大小选择,要从熔融料的黏度、成型制品的形状、塑化条件、成型模具的温度及制品外形尺寸精度要求等因素考虑。注射力选择得过大,塑料制品成型时容易产生毛边,制品的内应力较大,而且脱模也要困难些。如果注射力选择得偏小,则容易造成被注射的熔料不能充满模腔,使制品不能达到要求的形状,有的即使成型制品,其外形尺寸精度也难达到质量要求。 表1中给出了塑料制品的尺寸精度要求和用料黏度要求不同时,需要注射成型制品的注射压力,供注塑成型时选择注射压力参考。
表1 制品尺寸精度和用料黏度与注射压力关系
塑料制品成型条件 注射压力/MPa 制品尺寸精度一般,原料黏度较低 70~100 制品外形有一定的尺寸精度要求,原料黏度中等 100~140 制品外形尺寸精度要求较高,原料黏度较高 140~170 制品外形较复杂,尺寸精度要求高 230~250
一般情况下,选择注塑制品用注射压力要大于注塑成型制品用压力的20%。 对注塑机的注塑压力调整,可采用调换注塑机中螺杆(柱塞)直径的方法。这是因为由于液压系统的额定压力和注射油缸的压力值不变,而螺杆(柱塞)得到的最大推力也是恒定不变值。 不同螺杆(柱塞)直径与注射压力的关系是

式中 D1——第一根螺杆(柱塞)直径,mm; P1——第一根螺杆(柱塞)的注射压力,MPa; Dn——调整后螺杆(柱塞)直径,mm; Pn——调整后螺杆(柱塞)注射压力,MPa。
|
|
|
|
理论注射量是指注塑机中的螺杆(柱塞)在一次最大行程中注射装置所能推出的最大塑化熔料量(cm3)。理论注射量是注塑机的主要性能参数。从这个参数中可以知道注塑机的加工能力,从而可确定一次注射成型塑料制品的最大质量。 国家标准GB/T 12783—1991中规定,理论注射量的大小用物料熔融状态时质量(g)或容积(cm3)表示。目前,国内和世界各国用容积(cm3)标注方式较多,因为物料容积与物料熔融状态的密度无关,此种标注方法适应于任何塑料的计量。 理论注射量计算公式为
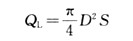
式中 QL——理论注射量,cm3; D——螺杆(柱塞)直径,cm; S——螺杆(柱塞)的最大行程,cm。 由于螺杆(柱塞)外径与机筒内径之间有一个相互运动的装配间隙,当螺杆(柱塞)推动熔料前移时,受喷嘴口直径缩小和物料与机筒内壁摩擦等阻力影响,会有一部分料从间隙中回流。另外,熔料冷却时会有一定收缩量需要补充。所以,注塑机的实际注射量要小于理论注射量,计算时需要用系数K值修正,K值的大小与螺杆(柱塞)的结构及参数、外径和间隙、注射力的大小、熔料流速、背压大小、模具结构、制品形状和塑料的性质等因素有关。当螺杆头部有逆止阀时,取K值为0.9;如只考虑熔料的回流时,取K值为0.97。 即实际注射量

如果知道塑料制品的质量,在选择注塑机时,则熔融状态下塑料的容积换算为密度。即

式中 Qs——注塑机实际注射量,g; ρr——塑料熔融状态下的密度,g/cm3。 塑料在不同温度条件下的密度见表1。
表1 塑料在不同温度条件下的密度
名 称 室温下密度/(g/cm3) 加工温度/℃ 熔融状态下密度/(g/cm3) 聚苯乙烯(PS) 1.05 180~280 0.93~0.98 低密度聚乙烯(LDPE) 0.92 160~260 0.73~0.78 高密度聚乙烯(HDPE) 0.954 260~300 0.71~0.73 聚甲醛(POM) 1.42 200~210 1.16~1.17 尼龙6、尼龙10(PA6、PA10) 1.08 260~290 1.008~1.01 聚丙烯(PP) 0.915 250~270 0.72~0.75
如果按塑料制品的单件质量选择注塑机的型号(注意:塑料制品的单件质量应是注塑机理论注射量的70%~90%),选择这种型号的注塑机生产此塑料制品为最佳方案。如果塑料制品的质量小于注塑机理论注射量的40%,用这台注塑机生产此塑料制品,则既降低注塑机的设备利用率又大大提高了此塑料制品的生产成本。
|
|
|
|
模板行程尺寸的大小由注塑制品的高度和成型模具(移动部分模具)的厚度尺寸来决定。一般条件是模板的行程距离大于移动模具厚度尺寸的2倍,以开模后能取出注塑制件为准。图1所示为注塑机模板行程距离与注塑件及成型模具的尺寸关系。为了缩短注塑件的生产循环时间,提高生产效率,应注意调整模板行程,使其在能取出制件的条件下越短越好。
图1 模板行程与制件尺寸的关系 1—固定模板;2—固定阴模;3—注塑制品;4—移动模板和阳模
图1中,L是模板的最大行程(间距)。在液压机械式合模机构中,固定模板与移动模板间最大行程(间距)等于移动模板的工作行程与固定模具最大厚度值之和,即

|
|
|
|
成型模具在设计时,首先要由注塑件的高度尺寸来设计决定模具厚度,然后再按注塑机上模板的最大行程尺寸来核对。从图1中可以看出:如果固定成型模具中的阴模部分厚度小于δmin值时,装配固定模具时要加垫板,否则注塑合模时会损坏机械零件;如果这个尺寸大于δmax值,则这台注塑机将不能合模工作。
图1 模板行程与制件尺寸的关系 1—固定模板;2—固定阴模;3—注塑制品;4—移动模板和阳模
在液压机械式合模装置中,设计成型模具时,一定要注意控制固定模具(阴模)厚度的最小值与最大值;模具厚度尺寸的最大值与最小值之差值,就是合模机构模具安装调整的最大尺寸。
|
|
|
|
HDPE包装桶成型工艺条件控制要点有哪些? (1) 原料处理。由于PE属于非极性聚合物,所以一般不吸湿,因此PE原料在吹塑成型前不必干燥,只要根据制品的要求进行染色(或用色母料)或不染色。 (2) 料筒温度。在保证挤出型坯光滑的情况下,尽可能采用较低的加工温度。温度过高会引起熔体强度下降而使型坯下垂,造成型坯纵向壁厚不均,而且使冷却时间加长,延长成型周期。但是,温度过低,则制品表面光泽度差,并增加内应力。一般HDPE的料筒温度控制在150~210℃。
(3) 吹塑压力。为保证型坯紧贴模腔壁而得到所需形状的制品,吹塑压力一般控制在0.5~0.65MPa之间。对于容积大、桶壁较薄的容器和MFR较低的树脂,吹塑压力要高些,反之则相反。 (4) 吹胀比。一般HDPE桶的吹胀比在(1.5~3):1之间。容器较大、桶壁较薄的容器选择较小的吹胀比,反之亦然。
|
|
|
|
型坯的设计,包括型坯的外形及型坯芯棒外形的设计。聚乙烯药瓶多是圆形回转体,其基本瓶形的结构如图7-3所示。瓶可分为瓶口(型坯口)、瓶颈(型坯颈)、瓶肩(型坯肩)、瓶身(型坯身)、瓶底(型坯底)等部位。 (1)型坯外形的设计。一般的聚乙烯药瓶,其容量为60-IOOmL,根据瓶的外形尺寸及表7-9提供的参数,设计型坯的外形(图7-4)。
项 目 选取参数 型坯口至型坯颈的距离/mm 50 70 瓶的质量/g 9-10 13-15 型坯底部与瓶底间的距离/mn 1.5 ~2 3-4 型坯高度H坯m H坯=(0.92-0.95) X瓶髙 型坯底部直径φ坯底/mm Φ坯身=(0.54-0.58 X瓶底直径 型坯身外径φ坯身/mm Φ坯身=瓶身外径/吹胀比 型坯肩部高度H坯肩/mm H坯肩=(0.20 -0.25) X瓶肩高度 型坯口外径φ坯口/mm Φ坯口=瓶口外径 型坯颈部圆弧R坯肩/mm R坯颈=5-10 型坯底部圆弧R坯底/mm R坯底=3-6 型坯肩部圆弧R坯肩/mm R坯肩10-20 (2)芯棒外形设计。芯棒是型坯模具的关键部件,相当于型坯模的阳模,它决定了型坯的厚度和内表面形状。设计中的芯棒高度,指瓶口到芯棒底的距离,即型坯高度减去型坯底部厚度的距离。其余部位的设计参数如下: 瓶口部位芯棒直径Φ芯口=瓶口外径-2X瓶口壁厚 =瓶口外径-2x(2~3) 芯棒底部圆弧Φ芯底=3mm(瓶重在15g以下时), Φ芯底=4mm(瓶重在15g以上时) 芯棒肩部上圆弧半径R芯肩上=R坯径+ (2 ~ 5) 芯棒肩部下圆弧半径R芯肩下=R坯肩+(3~6) 型坯底部的厚度=瓶底的最小厚度+瓶重xO. 1 |
|
|
|
药瓶生产工艺流程如下。 材料混合→物料塑化→注射→开启型坯模→型坯及芯棒转位吹塑模具闭合 包装 ←药瓶火焰表面处理 ←药瓶脱膜 ←开启吹塑模 ←型坯吹胀冷却┛ |
|
|
|
(1) 材料的选择。吹塑成型的聚乙烯,一般为髙密度聚乙烯,有较好的力学性能和耐应力开裂性能,有较好的卫生性能,其钛含量<80mg/kg,MFR =0.3-〜0. 7g/10min ,p = 0. 950g/cm3;钛白粉或乳白母料,着色力强,分散性好;硬脂酸锌,有较好的润滑性能,以提髙型坯的光泽及脱模性。兼具热稳定作用,防止白色药瓶变黄。 (2) 配方。 HDPE IOOkg 硬脂酷锌 0.2~0.3kg
乳白母料(钛白粉含量>75% ) 2〜3kg
|
|
|
|
1) 超声波抛光的设备 超声波抛光设备主要由超声波发生器、超声换能器、机械振动系统、机床本体等部分组成。 1) 超声波发生器。它的作用是将50Hz的交流电转变成具有一定功率输出的超声波电振荡,是超声波抛光的动力源,在模具加工中多采用晶体管式和集成电路式超声波振荡发生器。 2) 超声换能器。它的作用是将高频电振荡变为高频机械振动,目前常用的有压电效应式和磁致伸缩效应式超声换能器两种形式。前者是利用在锆钛酸铅介面上加上电压后,则会产生相应的机械波;而后者是利用铁、钴、镍等合金磁性材料在高变磁场作用下,其尺寸发生伸长和缩短这一特性而产生高频机械振动。 3) 机械振动系统。机械振动系统包括变幅杆和工具。变幅杆又叫振幅放大器,它能将超声换能器产生的振幅加以扩大,以满足超声加工的需要。变幅杆的形式有圆锥形、指数形、阶梯形等。工具是直接将超声波传递给工件的零件,它与变幅杆固定在一起,工具头部应与型腔的形状相适应。 4) 机床本体。是机器的基础部件,主要包括工作台、立柱、工作头、工作液循环系统等。工作台是安放工件的地方,可作纵横调节,工作台上带有盛磨料悬浮液的工作槽,悬浮液在其循环系统的带动下能在加工区域内得到良好的循环。工作头可用来调节工具的进给压力和进给速度,并定期上升,以便更换加工区磨料。工作头是由立柱带动作上、下运动的。 (2) 超声波抛光的操作 1) 抛光余量的选择。抛光是型腔的一种精加工方式,因此抛光余量不能太大,一般控制在不大于0.04mm,过大则难以达到要求。 2) 抛光操作。为了保证抛光质量,一般要经过粗抛、细抛和精抛等三道工序。 ① 粗抛。粗抛时可采用固定磨料,如金刚石油石、刚玉油石、电镀金刚石锉刀等;或较粗粒度(180#左右)的磨料进行抛光。 ② 细抛。细抛时采用游离磨料方式,磨料可用氧化铝、碳化硅等,其粒度为W40左右。工作液用煤油、汽油或水。 ③ 精抛。精抛为最后的抛光,可采用评W5-W3.5粒度的磨料进行抛光,一般不加工作液,干抛即可。 (3)抛光时的注意事项 1) 在每次更换磨料时,都应将工具头部和抛光表面清洗干净。 2) 采用诸如机油、煤油等矿物油作工作液,比用水作工作液时抛光的质量要好。 3) 抛光时余量不能太大,若余量太大,则需耗去大量时间,大大影响生产率。 4) 磨料与工作液之间的重量比应控制在合适的范围内才有利抛光,一般为0.5~1.0左右。 5) 工具的振幅应控制在0.01~O.lOmm,频率控制在1.6~2.5万Hz之间, 抛光频率应尽量接近共振频率,以取得最大振幅,这样效果才好。 6) 工具与工件之间的间隙和静压力对抛光质量和生产率有较大关系,为找到其最佳值,常要作多方尝试,以确定合理的间隙和静压力。 7) 被加工材料不同,磨料的种类也不同,因此要根据需抛光的材料来选择磨料种类。 8) 磨料粒度的选择与振幅有关,当振幅为0.05mm时,粒度越大,生产效率越高;当振幅小于0.05mm时,粒度越小,加工效率越高。 |
|
|
|
1) 注射机加热温度:加料段220〜235℃ ,压缩段230〜240℃ ,计量段235 -250℃; (2) 注射机喷嘴温度:240〜250℃ ; (3) 型坯模具温度:瓶口部位75 ~ IOOcC ,瓶身部位100--110℃ ,瓶底部位100~50℃; (4) 型坯吹胀比:(1.6~2.0) :1; (5) 吹塑模具温度:10〜---30℃; (6) 型坯注射压力:(20〜--22) XlO5Pa; (7) 型坯吹胀用压缩空气压力:0. 8-1. OMPa; (8) 瓶表面处理,火焰与瓶表面距离约12 ~ 13mm,瓶能自动翻转90。 |
|
|
|
塑料球的原料选川低密度聚乙烯,中空级适当惨入高密度聚乙烯5% ~ 15%(质量分数),用以增强制品的物理性能,调整原料的流动性 |
|
|
|
(1) 挤出机。单色球选用蟝杆直径为45mm左右的挤出机即可。双色球选用两台螺杆直径为45mm左右的挤出机。长径比为20::1,压缩比大致为(2~4)1. (2) 机头。采用转角机头,机头内流道有较大的压縮比,口模部分有较大的定型模。 (3) 模具。中空球模具一般用铸铝制成,夹口嵌件用优质钢经热处理制成,型腔经喷砂处理。 |
|
|
|
(1) 生产工艺流程。塑料球生产工艺流程如下。 聚乙烯→挤出型坯→吹胀成型→制品 (2) 工艺参数。按工艺条件,首先将挤出机料筒和机头加温,达到要求后,将原料和颜料搅拌均匀投入挤出机料斗,启动挤出机,物料经塑化从机头挤出壁厚均匀、光滑管状的型坯。型坯挤够长度时,辅机立刻启动、合模,模具的上下口把管坯夹在模具中,模具上方的割刀把管坯切断,并迅速退回原位。模具夹着管坯移到定位,气针通过模具插入管坯中,压縮空气通过气针将管坯吹胀,断气退回气针,熔融料密封针孔痕迹,开模取出制品。制品出模后,加以修整即可装箱。 双色球的生产工艺是采用两台分别装有不同颜色原料的挤出机,共用一个机头同时挤出。通过该特殊机头,即可得到直纹、双色、壁厚均匀的型坯,再经合模吹胀而成。
在吹塑成型过程中,应注意对挤出机料筒、机头和模具的温度控。温度过髙或过低都不能得到合格的制品,甚至无法正常生产。料筒三段温度分别控制在110~120℃、130~140℃和140~150℃,机头温度控制在140~150℃和150~160℃ ,模具温度控制在4~20℃。吹胀比为1:(2~4),吹胀压力为0.2~0,69MPa。
|
|
|
|
中空吹塑盘一般以高分子量高密度聚乙烯为主要原料,可加人20% ~30%的自身回收料,并可根据产品的不同用途添加1%-2%的功能性母粒。 HDPE的性能主要取决于其密度、相对分子质量及相对分子质量分布三个因素。密度越大,制品的刚性和硬度越髙,耐化学腐蚀能力越强;相对分子质量越大,聚合物流动越慢,韧性和耐环境应力开裂性就越好;相对分子质量分布的宽窄则会直接影响聚合物流动的快慢。 目前生产中空吹塑托盘使用的HMWHDPE是在低压(0.31―0. 48MPa)和低温(80~1I0cC )下,以过渡金属为催化剂使乙烯聚合而成的,通常为线型共聚物或均聚物,其重均分子量为20万〜50万,密度为0. 944 ~ 0. 954g/cm3 ,高载荷下熔体流动速率为1 ~ 15g/10min。由于HMWHDPE兼具产品制造时对聚合物各方面的综合要求,尤其是它的高分子量使其具有极优良的韧性和耐环境应力开裂性,可抵御众多化学品的腐蚀;而它的高密度赋予产品足够的刚性和硬度。再加上其适中的相对分子质量分布可明显降低高分子量聚合物在流动中的难度。
|
|
|
|
中空吹塑托盘的生产工艺类似于箱包生产,比桶类中空制品的生产工艺简单。中空吹塑托盘的生产工艺流程如下。 树脂┓ →共混→造粒→功能母粒┑ 助剂」 HDPE┓ ↓----------------- ------- 色母粒 →共混→塑化挤出→吹塑定型→后加工→制品 表7-10列出它的工艺条件。在表7-10的工艺条件下吹塑成型 托盘的生产周期为300~360s,其中冷却时间为140~160s,排气时间为60 ~80s,卸压时间为65 - 90s。
项 目 一段 二段 三段 四段 机筒温度 挤出机1 195 -220 190-210 195 -220 195 -220 挤出机2 190-210 195 ~220 195 ^220 195 ~220
机头温度①/℃ 190~210(1段)195 ~220(2〜9段) 冷水温度/℃ 13 -16 吹塑压力/MPa 0.4-0.5
|
|
|
|
(1)中空吹塑托盘的优点如下。 ① 投入资金少。用大型挤吹中空成型机生产中空吹塑托盘,一机多用,降低投资成本,且模具成本低,投资少。 ② 外形美观。根据制品承重的特点,从力学原理人手,在模具上设计不同排列形式的圆形立柱及不同方向的凹槽,使制品表面带有防滑颗粒,由于使用冷冻水快速冷却,使制品表面平整,有较高的尺寸精度。 ③ 性能优良。制品经挤出吹胀一次成型,成型过程快速,物料在高融状态快速吹胀冷却定型,可消除内应力,使制品内在质量和性能稳定,符合国家标准要求。 ④ 安全性好。不助燃、不导电、防滑、无毛刺飞边、无其他辅助连接,可确保货物和作业者的安全。 ⑤ 寿命长。制品通过添加防老剂可提高户外使用寿命,一般条件下可用5年以上;恶劣环境下可用2年。使用寿命为木托盘的5~7倍、钢托盘的2 ~3倍。 ©环保性能好。制品无毒无味,耐酸碱盐的腐蚀,易于清洗消毒,不腐烂,同时废旧托盘可回收利用,符合环保要求。 ⑦ 运输成本低。托盘质量轻,可大幅度降低集装箱货物运输时的费用,进行对外贸易时,出人境无需像木托盘那样由卫生检疫部门进行熏蒸、消毒等处理。 ⑧ 维护费用低:塑料托盘不需要修理、保养,即使外表损坏,只要内部的立柱黏结完好,就不影响正常使用。 ®适应性强。中空吹塑托盘双向四向均可操作,又有双面、单面两种形式,可用于各行各业,提高工作效率和空间利用率。 ⑩承载能力强。由于托盘按受力情况合理地进行了结构设计,使得承载能力强,均匀分布的承载能力为:静载荷30~40kN,动载荷20-30kN,架空载荷为IOkN。 (2)中空吹塑托盘的缺点如下。 ① 后加工工序复杂。中空吹塑托盘的后加工工序较复杂,每个制品的飞边(约占制件总重的30%)都需要修整,而修下的大量飞边要进行分割、破碎工作,且每个制品在冷却24h后还要用电鋸削切叉口,产生的边角料也要进行粉碎。 ② 生产效率较低。生产中空吹塑托盘时虽采用冷冻水冷却,以提高制品质量和生产率,但因制品有较大的飞边,整体消耗原料较多,这就要求设备有足够高的塑化能力,以缩短成型周期。中空吹塑托盘成型周期较长,一般每个周期为5~6min;而注射成型托盘每个周期约为3min,相对而言生产效率较低。 ③制品刚度较低。由于成型方法不同,中空吹塑托盘的刚度不如注射托盘,虽可通过添加增强剂来改善制品的刚度,但填充增强剂又会加快设备螺杆的磨损。 |
|
|
|
(1)必须经常检查注料启动保护控制系统,保证可靠。 (2)操作结束时打开模嘴,注射到底。操作开始时必须检査模嘴是否处于开口状态。冷料加热至设定温度,保温1h,然后在50%系统工作压力情况下点动模嘴开关液压缸,模嘴开关正常后使模嘴处于开口状态。然后检查机筒冷料是否至设定温度,并符合保温0.5h的要求,达到条件后,点动预塑,模嘴有熔料流出,方可投入正常成工作。
|
|
|
|
(1) 原料塑化熔融时工艺温度应控制在170~ 230℃范围内。 (2) 坯管吹塑成型瓶制品用吹胀比控制在(1.5~3) :1范围内。 (3) 吹胀坯管成型瓶制品用压缩空气压力为0.3 ~0.6MPa。(4) 成型瓶用模具温度为20~50℃,冷却定型时间约占制品成型生产周期总时间的50%~60%。 (5) 瓶制品的质量要求是:制品表面光洁,在阳光下检查无色差、变色和色泽不均匀等缺陷;瓶内装满水后旋紧盖,从1.2m高处坠落3次无破损、不裂底。 |
|
|
|
1)混料机。混料机用于PVC树脂与添加剂的捏合、混合,制取用于吹塑成型的PVC干混料。常用的混料机有高速混合机、热冷式混合机。 髙速混合机(图7-15)由混合锅、搅拌叶轮、折流板、机盖、排料口、传动及控制装置组成。适用于热敏性塑料及不宜经受长时间热浪合物料的混合。混合机在高速运转时,可产生如下作用。
① 高速旋转的叶轮与物料的摩擦力以及锅壁对物料的反推力,使物料沿叶轮作切向运动。 ② 物料沿叶轮高速旋转产生离心力。 ③ 折流挡板使无规则运动的物料,形成涡流。 上述作用,使锅内物料进行交叉混合,同时,快速运动的物流,因摩擦而使料温升高,完成物料的混合。
热冷式混合机(图7-16)由高速混合机、平台、冷混机组合而成。
冷混机多为大容量、高冷却效率的螺旋搅拌机,其混合强度较低,但可使热混合物料快速冷却。经热冷式混合机混合的物料,其排料温度可降低到储存温度(40-60 ℃)。 (2)挤出造粒机。经混合的硬质PVC干混料,可直接用于成型加工,有时需制成颗粒状后使用。PVC干混料的挤出造粒,主要有拉条冷切粒和冷风热切粒两种。
拉条冷切粒,包括单螺杆挤出机、冷却水槽、切粒机(图7 - 17)等。若造粒时的环境温度不高,也可不采用冷却水槽,料条经空气冷却后,切成粒料,该切粒生产线的设备简单,售价低。 冷风热切粒,包括挤出机、切粒机(图7-18)、冷风装置等。挤出机可用单螺杆挤出机或双螺杆挤出机;双螺杆挤出机应选用混炼效果较好的啮合平行异向旋转双螺杆挤出机或啮合平行同向旋转双螺杆挤出机。双螺杆挤出机比单螺杆挤出机有更好的混炼效果和高产量(螺杆的转速可达200~300r/min)。但是,双螺杆挤出机售价高,较适用于大批量的粉状树脂造粒。冷风热切粒的旋转切刀,紧贴机头口模,安装在切粒罩内,切粒罩内鼓入冷风;为防止热切粒时粒料黏结在机头处,冷风机应有足够风力,并及时将热粒料输送到冷却储槽,粒料应冷却到室温后方能包装;为防止机头口模处的多孔模板被冷风冷却,应在模头处安装隔热装置。
硬质PVC干混合料的造粒方法,还有干热切粒、双辊机混炼一平板切粒等。 挤出吹塑瓶的边角回料较多,为降低物料损耗,应考虑将瓶的夹坯余料、边角及废品破碎后使用。破碎的边角回料,可直接用于成型加工,也可经挤出造粒后使用。经破碎的边角回料,一般用于不透明或半透明硬质PVC瓶的成型。 (3) 挤出吹塑机。硬质PVC透明瓶,一般采用未增塑或仅含少量增塑剂的PVC干混料或料粒成型,为使瓶的成型有较好的透明度、长期稳定的加工性,应使用专用的挤出,塑成型机,并满足如下
① 能使物料在较低的加热温度下混炼成均匀的熔体。 ② 从物料的挤出到型坯形成的整个过程中,应能使熔体流动畅通无死角;熔体在机内停留时间应越短越好。 ③ 挤出机的主要零部件、机头、模具等,应选用防腐蚀材料制作。 ④ 挤出机对物料的剪切作用均匀,强烈剪切作用的时间要短。 ⑤挤出机、机头应能快速地升温或降温。 ⑥挤出机、机头模具型腔等与熔体接触的表面,应加工光滑,防止熔体黏附;模具型腔同时具有良好的排气性能。
硬质PVC透明瓶成型,一般选用单螺杆挤出机,采用等距不等深渐变尖头螺杆,螺杆长径比(L/D>)为(20-25) :1,螺杆压缩比为(1.8 --2.5) :1.
挤出机螺杆的直径,一般选用45~60mm,大直径的挤出机加工硬质PVC瓶,成型稳定性差,物料易降解。 型坯成型机头,一般采用中心进料直角机头(图7-19)。为提高产量,降低瓶的生产成本,常使用双型坯或多型坯直角机头。不过,型坯头数越多,型坯壁厚均匀性越难控制。 PVC瓶的模具,最好选用铜铍合金、不锈钢制造。模具型腔不仅要经抛光,具有镜面光洁度,同时要有良好的排气性能。为防止氛化氢对模具的腐蚀,平时应注意对模具的维护保养。 (4) 空气压縮机。空气压缩机能提供0.2-1.OMPa的压缩空气。
|
|
|